从现场写实中“挖”出“效益花”
6月4日早8点,刚刚开完早会的河钢集团张宣科技球团公司王建成就急匆匆地赶到原料厂,跟踪督导车辆进厂、计量、卸车、堆存信息等各个环节工作,严把原料进厂第一道关口。
这是该公司推行“现场写实”的真实写照,为深挖降本潜力,球团公司将精益原料管理作为挖潜增效的“重头戏”,通过对物料流转环节顺序精细控制,从进厂、卸车、收料、储存环节;从堆放、规整、铲装、配料计量、倒运环节等对原料造成的损失,成立了原料损耗率再降低攻关组,开展现场写实,量化差距、量化目标、量化措施,最大限度降低原料损耗率,提升现场管理水平。
这车料几点进的,写实表上看一看;数量是多少,写实表上对一对;原因出在哪,写实表上找一找。球团公司狠抓现场写实工作制度的落实,动态跟踪,原料何时进厂,何时卸车,堆在哪里等量化数据体现在全流程、全过程、全方位,通过缜密分析,细致梳理,原料进厂、计量、供出等各个环节,促进原料损耗率持续改善。
现场写实对整个工作日内的生产情况及其时间消耗,按时间先后的顺序连续观察、如实记录,并进行整理、分析,“全时态”记录原料的工作节点,更准确地掌握原料进厂和卸车的节奏及动态,找出问题所在,调整工作重心,集中优势资源,靶向组织落实,提前规划卸料货位,降低原料损耗率。
“现场写实好,每一个细节动态跟踪生产,避免挖潜盲区。”王建成作为现场写实的直接操作者深有感触,他指着不同大、小堆的物料介绍到:“在消化物料的过程中, 本着‘先小堆后大堆、先散堆后整堆’”的吃料原则,严格规范吃料,地面标记以上物料全部消化,杜绝产生“小堆料”等静置物料。通过规范吃料,既减少了底子料的产生,又提高了原料的可用率。”
现场写实,数据在一线掌握,问题在一线发现,措施在一线制定,差距看得清,目标瞄得真,措施定得准,成为扩大挖潜增效的“金钥匙”。据悉,5月份,通过现场写实,原料损耗率降低至0.7%,实现挖潜3万余元。(刘震)
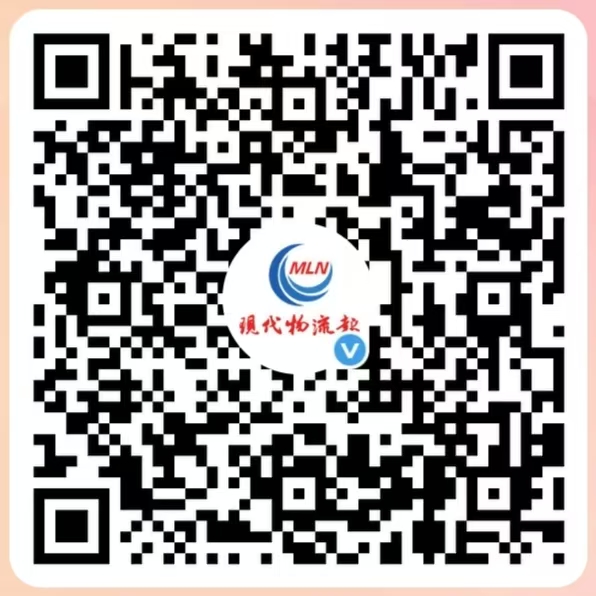
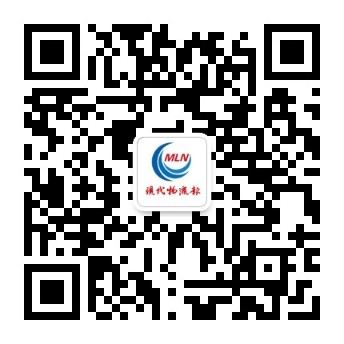
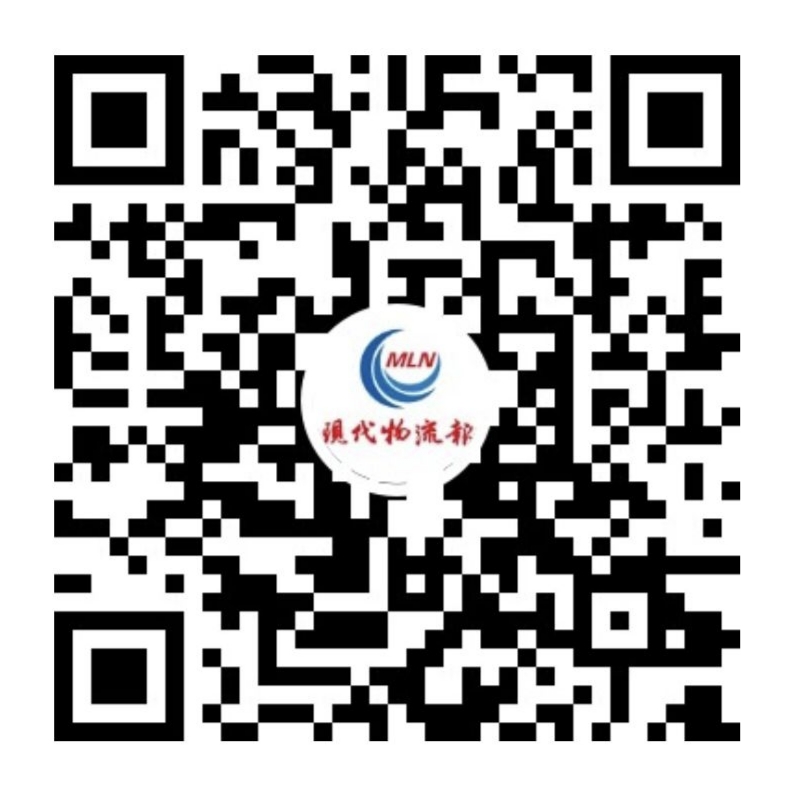
相关文章: