大型LNG运输船驶向产业深海
图①:中国自主建造的首艘大型LNG运输船“大鹏昊”。
图②:沪东中华首席技师秦毅在MARKⅢ型液货舱模拟舱底进行焊接。
图③:第五代“长恒”系列大型LNG运输船效果图。
强国建设,必经略于海洋。作为建设海洋强国的重要基石,船舶建造考验着一个国家的产业水平和供应链能力,高技术船舶建造更是我国船舶工业转型升级的重要方向。
从仿制引进到自主创新,从建造散货船、集装箱船等常见船型,到摘取世界船舶工业皇冠上的3颗“明珠”——航空母舰、大型邮轮、大型LNG运输船,中国船舶工业通过不断的技术升级推动产业升级,掌握了一大批关键核心技术,展现出强劲动能和勃勃生机。近日,记者来到国内首家具备大型LNG运输船自主建造能力并有实船交付业绩的船企沪东中华,且看这颗“明珠”如何绽放光彩。
——编 者
暗夜的海上,广东深圳大鹏新区大鹏湾东北侧,蓝丝绒般幽深的夜空与平静的海面融为一体。
波澜乍起,信号灯由远及近。一艘庞然巨轮在小型拖船的牵引下,缓缓靠泊,船体上的白色字母“LNG”格外醒目。船上满载的,不是普通散货,而是作为重要能源之一的易燃易爆化学品LNG(液化天然气)。
这艘名为“大鹏昊”的巨轮,是我国自主建造的第一艘大型LNG运输船,2008年4月交付投用,截至今年6月,已安全运载257船货物,累计交付约1670万吨LNG。
大鹏湾向东北1400多公里,上海东北角。横卧于长江出海口的长兴岛上,“大鹏昊”更多的“姊妹轮”在这里被建造出来。大型LNG运输船,船舶工业皇冠上的3颗“明珠”之一,已被中国船舶沪东中华造船(集团)有限公司(以下简称“沪东中华”)摘下15年,如今更加熠熠生辉。
去年,沪东中华承接大型LNG运输船订单达29艘,创造历史最高纪录。今年上半年,沪东中华累计交船9艘,新接订单金额逾200亿元,分别为年度计划的56%、72%;放眼中国船企,在全球大型LNG运输船的市场份额已经跃升至35%。
一个勇往直前的决定
建中国自己的LNG运输船
8月8日,立秋时节,长兴岛依然热浪翻滚。
驱车穿过上海长江隧道不久,便可见岛上各类吊机林立。再往位于东南角的沪东中华零号基地去,一艘总长295米、型宽45米、型深26米的巨轮映入眼帘,甲板上的工人忙碌有序,船头上“峨眉”二字苍劲有力。
“这艘17.4万立方米LNG运输船共有4个液货舱,最先施工的四号舱已经结束内壁作业,下一步准备安装泵塔,整船计划于今年12月交付完工。”沪东中华首席技师、国内首个殷瓦钢焊工秦毅告诉记者,目前仅零号基地同时在建的大型LNG运输船就有5艘。
回望24年前,LNG运输船对于沪东中华而言还是个陌生的名词。
1999年12月,国务院同意广东LNG试点工程总体项目一期工程立项,我国第一个进口LNG试点项目正式启动。当时要进口LNG,必须有配套大型LNG运输船,如果国内船企造不出,就只能花天价从国外购买。
消息传到沪东中华的前身沪东造船厂,领导班子炸开了锅。
争论的焦点在于,在前途未卜的情况下,厂里究竟要不要投入巨大人力、物力、财力,去配套建造一艘世界上没几个国家有能力建造的大型LNG运输船?更何况,当时厂里有很多员工连这种船都没见过。
“大型LNG运输船是供远洋运输零下163摄氏度LNG的专用装备。LNG易燃易爆,对船舶的安全性要求极高。”沪东中华副总工程师潘伟昌介绍,这种特殊的低温货物运输船是世界公认难度最高,具有高技术、高可靠性、高附加值的高端机电产品,代表了造船工业的最高水平,当时完全被国外船企垄断。
然而,时不我待,国家能源结构调整的重要一步已经迈开,这个窗口期怎能不抓住?
想“第一个吃螃蟹”,敢干更要会干。全方位培训、多层次交流、统一认识、下定决心、勇往直前……在充分的前期调研基础上,船厂的攻关工作紧锣密鼓展开。“在国外专家的指导下,厂里组织设计、生产、管理等部门数十人先试验建造薄膜型LNG运输船模拟舱。”潘伟昌说。
模拟舱具有3个方向的舱壁,相当于液货舱的一个角落。由于模拟舱完全按照实船工艺要求建造,对整个采购、装配过程的精度提出了极高要求,也让船厂遇到了难以想象的困难。
安装在货舱内起保温作用的绝缘箱,就像为LNG保冷的“棉被”,其外形胶合板的公差范围必须控制在0.1毫米之内。如果精度不够,安装不平整,会造成薄膜型内壁殷瓦钢受力不均,极易产生漏点,引发泄漏爆炸风险。
“当时,建造模拟舱只需100多个绝缘箱,数量少,要求又高,没有厂家愿意专门为我们配套。技术人员和采购人员踏破铁鞋,终于用诚意打动了上海奉贤的一家家具厂,对方用制造家具的机器设备,按照技术要求,开始试制绝缘箱。”潘伟昌回忆。
岂料一波刚平,一波又起。
绝缘箱做成了,一检测,总体精度要求达标,但局部精度还不够。怎么办?
“情急之下,我们就用砂纸一点一点手工打磨,直到精度完全达到要求。”潘伟昌说。
2001年9月,投资500多万元、历经7个月建造的模拟舱完成。国外专家带着各种设备,来厂里进行了非常严苛的检测,结果全部通过。
功夫不负有心人。几个月后,广东LNG造船项目在北京公开招标,厂里带着9大箱72本中英文对照的应标文件,成功中标!
厂里随之全面启动建造准备工作。为了找准切入点,加快研发进程,厂里在船体设计方面借鉴了法国大西洋船厂的技术,在特殊的液货舱围护系统上则引进了法国GTT公司的专利。
一切就绪,只待东风。
一次“从0到1”的突破
第一艘自主建造的大型LNG运输船“大鹏昊”如期交付
模拟舱建成了,专利也引进了,设计建造大型LNG运输船还有何难?
从码头边的临时台阶拾级而上,脚下江水滚滚,沿着3米多高的脚手架小心前行,记者来到靠近“峨眉”号船头的一号液货舱寻找答案。
液货舱围护系统,在储运LNG过程中发挥着隔热和密封的重要作用。如果说这个系统像一个保温瓶,液货舱的舱壁就好比保温瓶的内胆。
眼前这座液货舱,约10层楼高的十面体结构内,一条条焊接好的殷瓦板在作业灯照射下幽幽反光。站在舱底,如同置身充满科技感的未来世界。
“这就是大名鼎鼎的殷瓦钢,液货舱围护系统中直接接触LNG的材料。”秦毅告诉记者,这种钢材含36%的镍,热膨胀系数极低,从常温降至零下163摄氏度,几乎不会收缩、变形,相当稳定,但也极其“娇气”。
“舱壁所需的大部分殷瓦钢只有0.7毫米厚,薄如纸张,又极易生锈,在焊接中哪怕一个针眼大小的漏点,都有可能造成整船LNG泄漏爆炸。”秦毅说,“我们在焊接时,必须佩戴吸汗手套,如果有汗水滴在殷瓦钢上,20多小时后就会生锈。”
“看,那个在焊接的是我徒弟。”顺着秦毅手指的方向,只见一名头戴防护面具的焊工手持焊枪,正专注地躬身作业。
3米的长度,走路只需要几秒钟,可焊完这条搭接处的殷瓦钢焊缝,需要一个技术娴熟的工人全神贯注操作5小时以上。“焊接殷瓦钢,可以说比绣花还要精细。速度过慢,容易焊穿,导致绝缘箱等材料起火;速度过快,焊缝深度不够,容易出现漏点,一个漏点就是LNG泄漏的一个致命风险点。”秦毅说。
在“大鹏昊”上,全船焊缝长达130公里,虽然其中九成可以使用自动焊机作业,但剩下的角落只能由人工焊接,每一次操作都要确保“天衣无缝”。
“我那时被派到国外学习焊接技术,白天细心揣摩同行的动作、手势、速率、电流调节,晚上躺到床上,还经常用手比划,心里太着急了,就想早点学完回来。”当时只有25岁的秦毅,恨不得把一分钟当两分钟用,仅仅4周就通过了法国GTT公司的专业考核。
勤学苦练之下,殷瓦钢焊接难题终于被秦毅和他的徒弟们攻克了。然而,还有更多的工艺建造难题,如一座座大山横亘在时任围护系统管理科副科长黄华兵的心间。
“一艘大型LNG运输船,有特殊的液货舱围护系统、特殊的液货操控系统和特殊的推进系统等。特别是液货舱围护系统,有约50万个零件,是整个船体关键中的关键。”如今已是沪东中华总装二部党委书记的黄华兵告诉记者。
当时,虽然有国外船厂提供的全英文图纸和资料,但经常语焉不详,大家想照着操作如同老虎吃天,无处下口。
“我们成立了多个课题组,重新消化吸收所有图纸,从编制工艺开始一点点做起。”黄华兵感慨,“每一步都很难,每遇到一个难题,就要停下解决,两周能解决已经算快的。但每解决一个难题,就像中了大奖般高兴。”
2006年12月的一天,“大鹏昊”进入吊泵塔的关键环节,要将30多米高的泵塔垂直吊入液货舱内。为此,黄华兵和同事连续作战几周,才编制出一整套吊泵塔工艺方案。
按国外船厂要求,泵塔的起吊高度要达到60多米。但是沪东中华船厂的吊机吊臂限位高度仅56米,必须赶在黄浦江最低潮位的平潮期完成吊装,而这个时间窗口只有约1小时。
经过前期准备,早晨8点半,吊装工作开始。当泵塔从水平状态逐渐竖立起来后,大家发现,由于重心不在中心位置,泵塔并不垂直,无法正常吊入。黄华兵回忆:“当时国外的技术指导也在,但也想不到什么好办法。”甲板上站了不少人,但都鸦雀无声,焦灼的情绪在人群中蔓延。
窗口期只剩20分钟,第三次尝试开始。这次,泵塔的下端还是距离液货舱底中心大概半米。
“眼看着潮位就要涨上来,情急之下,当时的指挥长当机立断,直接吊进去,派人去舱底辅助。于是,我和十来个同事一起下到舱底,小心翼翼地将泵塔下端推到中心位置。推好后,吊臂还没松钩,潮位已经开始明显上涨,幸好有惊无险。有了这次经历,我们重新修改了工艺,为之后的类似操作蹚平了路。”黄华兵说,当年艰难探索出的各种工艺流程,后来也为国内其他船企建造大型LNG运输船提供了借鉴,推动了整个行业发展。
2008年4月3日,为广东LNG项目配套的“大鹏昊”正式交付。至此,被国外船企垄断多年的大型LNG运输船制造,终于由沪东中华破局。
一场没有退路的较量
“巴布亚”出口,中国大型LNG运输船驶入国际市场
2012年6月,正值梅雨天的上海,闷热难耐,让人止不住心烦意乱。
沪东中华时任LNG运输船主任设计师宋炜和团队在双艉鳍推进系统轴承问题上已经“卡壳”3个多月,厂里决定独立研发设计第二代17万立方米LNG运输船也已经过去快4年。
2008年10月,“大鹏昊”成功交付的喜悦刚过半年,宋炜看到一则新闻。“韩国建造出了第二代大型LNG运输船,不但船体容积从14.7万立方米一下子提升到17万立方米级别,推进功率和蒸发率也都更低。船上装备的新型低速机推进和再液化装置,是我之前见都没见过的。”他不禁心头一沉。
“不直面这场国际较量,费尽千辛万苦才落地的第一代船,恐怕很快会被市场淘汰,我们没有退路。”自主研发设计第二代大型LNG运输船的重任落到了当时34岁的宋炜肩上。
第二代船为什么能“吃得更少、跑得更快”?船体的心脏系统——推进系统升级换代很关键。为了提高LNG运输船大型化后的推进效率,韩国船企将第一代船的单艉推进改为双艉鳍推进设计。
“从单艉推进到双艉推进,并非技术上简单的一加一。双艉鳍线型艉鳍片体呈倾斜布置,完全不同于对称布置的单艉线型,两种类型推进的设计难度不可同日而语。由于两个艉鳍片体之间内侧、外侧的流场完全不对称,双艉鳍推进会造成两个螺旋桨之间的受力状态十分复杂,进而导致轴系的运行轨迹飘忽不定,容易引起轴承高温甚至轴系咬死的故障。一旦失去推进能力,发生海上事故,17万立方米满载的LNG运输船,就成了漂浮的海上炸弹。”宋炜深知,确保推进系统的高可靠性是新一代大型LNG运输船研发成功的基础。
究竟什么样的轴承设计结构才能保障轴系在复杂受力情况下安全运行?宋炜带着团队久攻不破。
然而,机会往往留给有准备的人。
有一天,不知是谁说了一句:“看,喇叭花开花了。”一筹莫展之际的宋炜抬头一看:“正好有一朵盛开在我眼前,花开的喇叭形状让我一瞬间联想到轴承的一部分可以另类设计的形状,立刻眼前一亮,随即召集团队进行设计。”
看似妙手偶得的背后,其实是无数的积累和反复的推倒重来。记者观察到宋炜别在左胳膊上的一支笔,他说:“习惯了,一有灵感,随时记下,说不定什么时候就能解决一个大问题。”
经过一系列计算分析和推敲论证,“喇叭口”式双斜坡轴承设计方案产生了。这样的形状可以让轴承适应不同载荷下可能出现的轨迹形状,最终形成涵盖各种极端恶劣情况下安全推进的双轴系推进方案。
攻克双艉鳍推进系统难题后,宋炜又带领团队攻克了第二代船蒸发气处理系统、液货处理系统等诸多难题。被问到有什么秘诀,宋炜笑了笑说:“就是专心致志、坚持到底去做,没有迈不过去的坎。”
2014年国庆假期,宋炜和同事们乘着我国第一艘自行设计建造、出口海外的大型薄膜型LNG运输船“巴布亚”,从黄浦江边的码头出发,一起出海试航。夜里,躺在轮机长办公桌做的“试航专铺”上休息,宋炜感慨万千,他在心中反复掂量这艘船的意义——
“巴布亚”在舱容、能效方面可与同时期日韩建造的最先进船型相媲美,能适应最恶劣的北大西洋海况,被租借给埃克森美孚公司。更重要的是,这次租借意味着中国大型LNG运输船终于走出了国门。
随后,第三代、第四代大型LNG运输船也陆续研发建造成功,在船型、主机、围护系统等方面不断升级,进一步打开了国际市场。如今,在零号基地,能耗指标、环保性能及可靠性均达世界顶尖水平的第五代大型LNG运输船“长恒”系列已经在建造中,带动了一大批国内配套厂商蓬勃发展。
潘伟昌介绍,建造“大鹏昊”时,国内配套厂商只有20多家。经过20多年发展,这个数字已经达到120多家。随着去年大型LNG运输船新承接订单井喷,未来几年,沪东中华将为国内配套市场带来数百亿元的产值。
一份坚定不移的执着
国产化率有望提升至70%以上
上料、切割、精修、打钉……走进沪东中华的绝缘箱生产车间,机器轰鸣声此起彼伏,作业人员有条不紊。只见这些绝缘箱外层为胶合板,中间填充淡黄色的玻璃纤维,看似平平无奇。
“一艘大型LNG运输船所用的绝缘箱有1000多个型号,精度要求极高。”车间相关负责人屈继强告诉记者,“2006年以前,绝缘箱如果全部靠进口,一艘大型LNG运输船所用的绝缘箱总价为400多万美元;国产化后由我们自己建造,造价几乎减半,供应也更有保障,仅这个车间的月产量就达到3万个。”
除了绝缘箱,3年前还要从国外进口的船用超低温阀门,如今已经由沪东造船阀门有限公司配套生产。“最新开工的大型LNG运输船,将全口径采用国产阀门。”企业董事长金宁介绍。
在沪东中华科技委主任金燕子看来,国产化率可谓国内LNG运输船产业由大到强的关键。“LNG运输船上的材料分为低温材料和常规材料。由于极致的可靠性要求,即使是常规材料也不常规,相关零部件的使用寿命要达到40年,这与一般的20—30年的要求相比有巨大提高,此外在精度上也有更高的要求。”金燕子说,国产化率提高,不但可以显著增强企业的议价能力,还能提升国际竞争力,保障产业链供应链安全。
15年前,第一艘“大鹏昊”LNG运输船交付时,国产化率只有20%多。2015年以来,在相关部门主导推动和国内船企的执着实干下,我国大型LNG运输船国产化率实现大幅提升,各项技术突破捷报频传。
2017年,由沪东中华牵头,联合宝武特冶等企业,仅用4年时间就研发出国产LNG运输船用殷瓦合金,即将用于实船。2022年,中国船舶集团旗下第十一研究所与沪东中华、江南造船组成联合专项研发团队,自主研发了MARKⅢ型LNG液货围护系统波纹板全位置自动焊接装备。
中国船舶工业行业协会发布的数据显示,2022年,我国形成了以沪东中华、大船重工、江南造船、招商海门和江苏扬子江船业为主的多个大型LNG运输船建造企业集群。
“对当前我国船舶工业来说,进一步加强产业生态合作,加快打造高水平、现代化船舶工业产业链供应链愈加紧迫。”中国船舶集团有限公司第七二五研究所党委副书记、所长王其红分析,“随着能源安全需求不断提升,国家有必要进一步出台相关政策,加大对关键材料和核心配套产品研发的支持力度。”
点火,开工!8月8日,沪东中华制造二部加工部件作业区产线,随着耀眼的火花四溅,大型切割机裁下首块钢板,将用于一艘17.4万立方米大型LNG运输船的建造。
这艘船由沪东中华自主研发设计,国产化率有望达到70%以上,建成后将成为国内国产化率最高的大型LNG运输船。据介绍,目前大型LNG运输船的专项科研也已启动,很多基本材料和装备的研发均在紧密攻关中。
“目前,国外最快的造船周期是18个月,在各方支持和企业努力下,我们已经接近这一目标。”沪东中华董事长陈建良介绍,如今企业手握大型LNG运输船订单量近50艘,工期已经排到2028年。
零号基地上,天高海阔,5艘进入码头周期的巨轮正在同时建造,蔚为壮观。登高西眺,沿黄浦江上溯数十公里,15年前,“大鹏昊”在南岸沪东中华的老码头一经诞生,四座皆惊。极目东望,滚滚长江奔流入海,将有更多中国建造的大型LNG运输船从这里出发,劈波斩浪,不惧风雨。
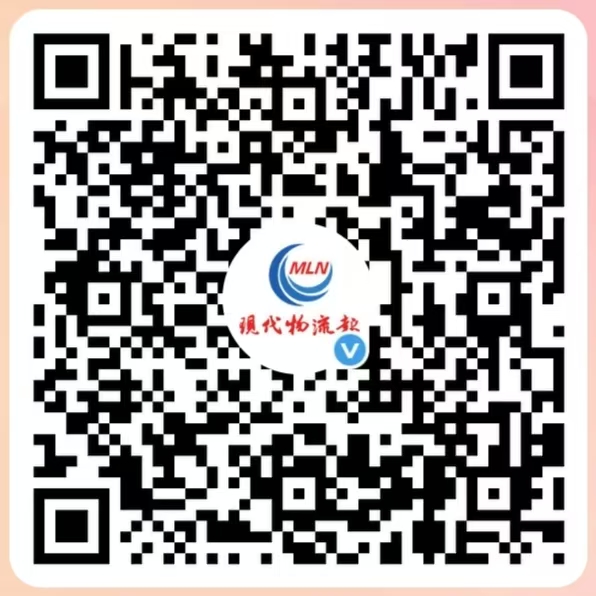
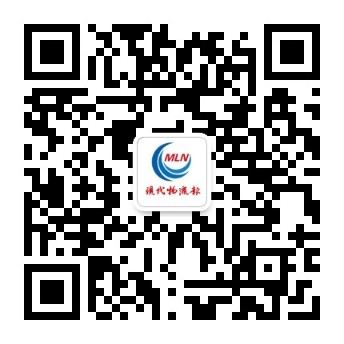
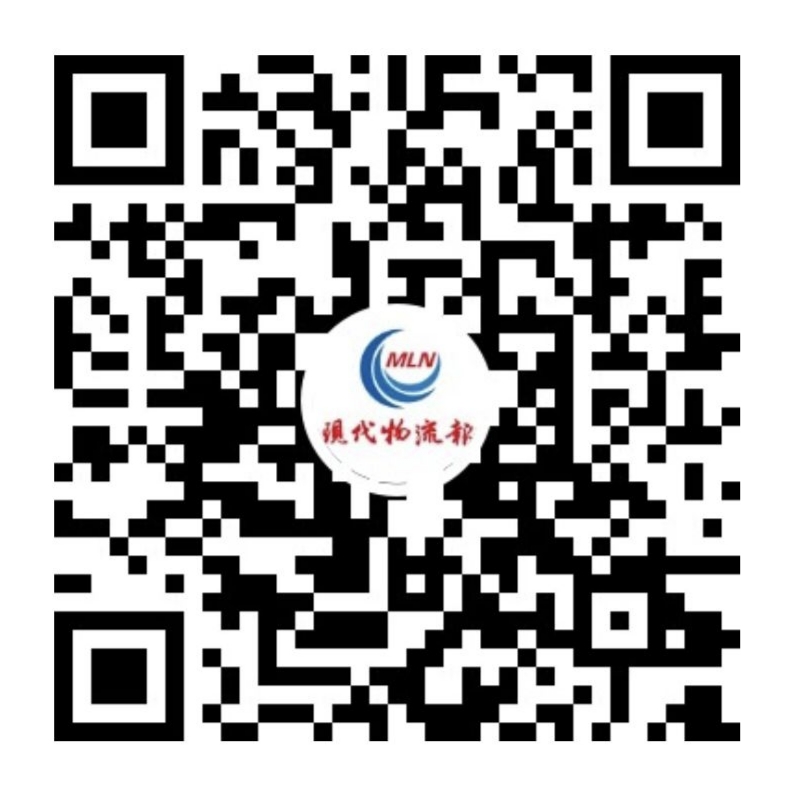
相关文章: