攻克机车防雨难题 单台年降本13.2万元
河钢集团张宣科技物流公司近日传出捷报:GK1E3280、GK1E3290型内燃机车电控阀箱防雨技术升级项目圆满完成。这项完全自主创新的技术升级项目,破解了困扰企业多年的雨季设备故障难题,实现单台机车年降本13.2万元,故障率同比下降95%。
作为畅通物流的关键设备,该公司三台GK1E改型机车因原厂设计高度受限,电控阀组被移至侧百叶窗下方,在解决机车限高需求的同时,也存在环境适应性不足的问题——雨雪天气时,水流通过百叶窗缝隙侵入设备舱,极易引发电控系统异常。升级前数据显示,年均发生23次相关故障,涉及70个电控阀和30块微机板的更换维护,单次故障处置最长耗时12小时,对原料运输效率和设备稳定运行形成制约。
面对这一技术难题,该公司组建专项攻关团队,在液传室仅0.8米高度的特殊作业环境下,创造性实施“空间重构+系统再造”升级方案。技术团队经过二十余次现场勘测,最终选定冷却室后墙距地板1米处作为新安装位,该位置不仅彻底避开雨水侵袭,更兼具管路连接便捷、检修空间充足、通风散热良好等优势。施工过程中,该公司技术团队采用长1米、宽0.7米、高0.5米的三角支架固定设备,同时应用φ6mm铜管快接技术,单台机车配置50米铜管和30个快接头,实现风管路直线连接。特别针对原铺设在液传室地板的7组控制线缆,升级为后墙内嵌式布线工艺,有效规避油水侵蚀风险,使电缆防护等级提升至IP65防水标准。
在成本控制方面,该公司技术团队践行“旧件复用、精准投入”原则,最大限度挖掘设备潜值。升级过程中,三角支架采用废旧钢材焊接制作,铜管快接系统通过优化管路走向减少65%材料消耗,单台改造材料成本控制在1.5万元以内。施工周期较同类项目缩短40%,仅用45天便完成3台机车升级。经连续三个月的运行监测,升级后电控阀组工作环境湿度下降85%,设备使用寿命恢复至设计标准的2年周期,微机板实现零烧损。
经连续三个月运行监测,电控阀组工作环境湿度下降85%,设备使用寿命恢复至设计标准的2年周期,微机板实现零烧损。经济效益核算显示,升级后的电控阀年更换量大幅下降,结合微机板零损耗,年可节约备件费用达13.2万元。运输效率也得到极大提升,故障处置时间从平均4小时压缩至45分钟,设备可用率提升至99.6%,2024年雨季期间实现零故障。此次改造形成的《电控系统防潮改造技术规范》已通过企业技术委员会认证,其三大核心技术具有行业推广价值。目前,该技术已在3台同型机车成功复制应用,预计全面推广后年度维修预算可压缩40%以上。
“此次技术升级不仅解决了设备问题,更形成了‘问题导向+自主创新’的技术研发机制。”该公司副经理张磊介绍,“我们正基于升级开发机车健康监测系统,计划年内实现温湿度实时监控、故障智能预警等功能。下一步,我们将重点攻关能耗优化、智能诊断等技术领域,推动物流设备从“机械化”向“数字化”迈进,为冶金行业绿色低碳发展贡献物流力量。”
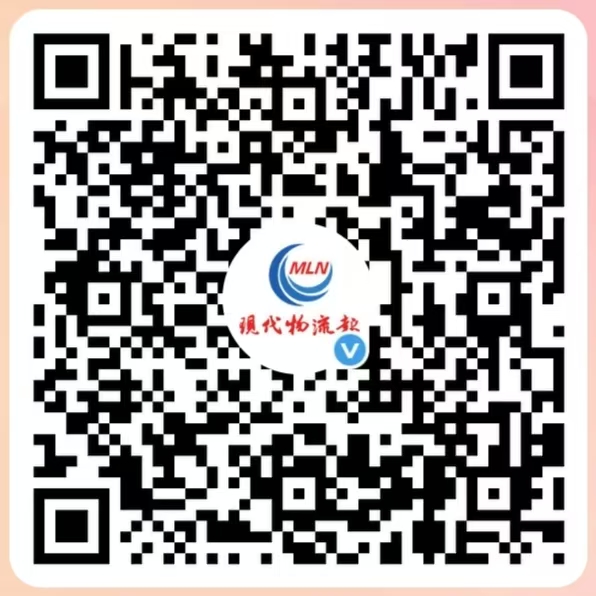
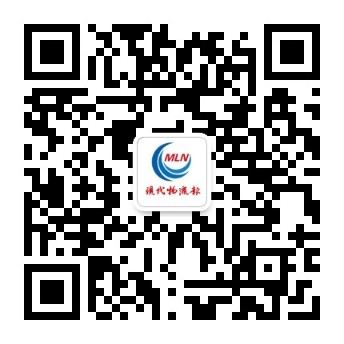
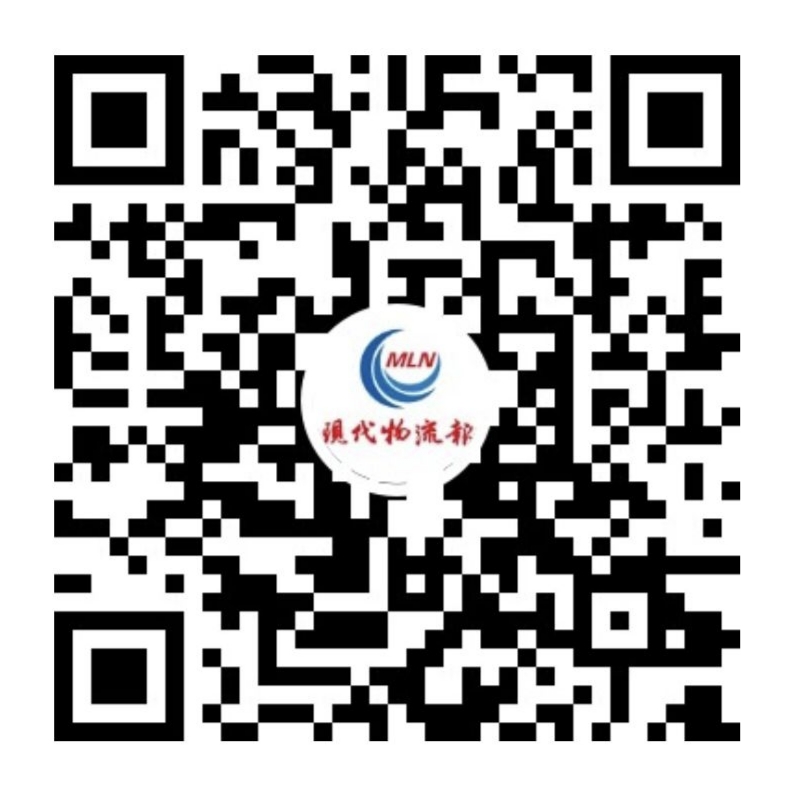