河钢集团张宣科技:双“变”破解高压水除磷降耗“密码”
“改变除磷压力,实施出炉辊道三段变速改造,双变同启,在保证除磷质量的同时,实现除磷设备电单耗较计划降低7.58 Kwh。”1月1日,河钢集团张宣科技金属材料公司型材作业区电气主管闫志东一语道出破解高压水除磷降耗的“密码”及成效。
四季度以来,该公司加强与石钢等行业先进企业对标找差,瞄准除磷设备等关键,以设备性能优化提升为着力点不断深挖能源降本潜能,持续推进产线高质高效低耗生产。
该产线高压水除磷装备位于加热炉出炉口与1架轧机之间,通过电机点动、逐步变频、气动驱动等系列操作清除钢坯表面氧化铁皮,确保特钢型材产品表面质量,投入使用以来除磷效果的大幅改善伴随着电耗的居高不下。怎样才能将耗电量降下来?闫志东和其他5名技术骨干成立了专项攻关团队,开始积极探索破题之道。他们先从电机降频开始,根据轧制道次不同,所需除磷效果不同,针对12.5#-20#五个规格特钢型材开展高压水除磷系统参数优化工作。
“先降5Mpa试试效果,36Mpa、31Mpa、26Mpa……”经过一个月的实践与论证,攻关团队找到除磷压力与电耗的最佳匹配方案,即停机时间超过 20分钟,复轧时前20支坯料除鳞压力降至30MPa,正常生产时后续坯料除鳞压力控制在30MPa-26Mpa区间内。在保证除磷效果的前提下,除鳞系统电耗降低0.06KWh/t。
“攻关取得初步成效,但与行业先进产线仍有一定差距,不妨换一个方向尝试下,通过增加小规格钢坯除磷时间,降低除磷压力推动电耗再挖潜。”攻关小组成员赵玉东提议道。有了新思路,攻关团队立刻投入到新的实验中,通过修改PLC程序,实现出炉辊道三段配速,前接加热炉高速出钢,后咬轧机高速进钢,中间低速经过高压水除磷装置,除磷压力虽然降低,通过增加停留时间,使钢坯表面氧化铁皮100%清除,除鳞压力降低至20MPa,设备单耗实现再降低。
“12月,除磷设备电单耗62.37Kwh,较计划目标降低7.58 Kwh,实现高压水除磷设备投入使用以来最低消耗,预计年可节费5万元。”看着电脑屏幕下降的曲线数据,闫志东自豪感倍增。
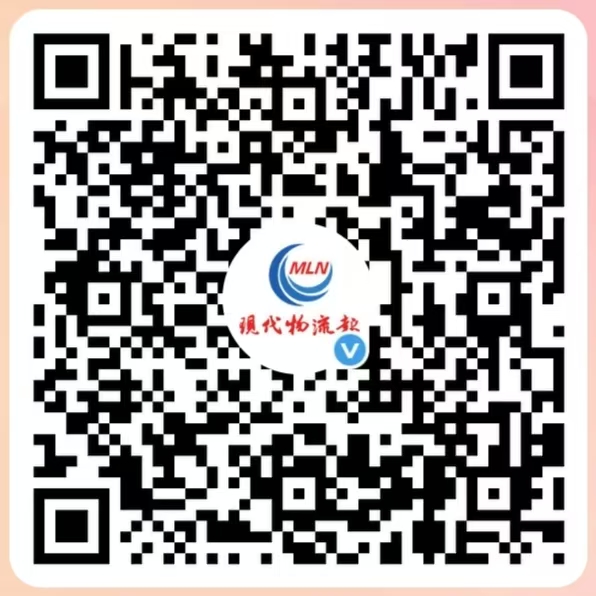
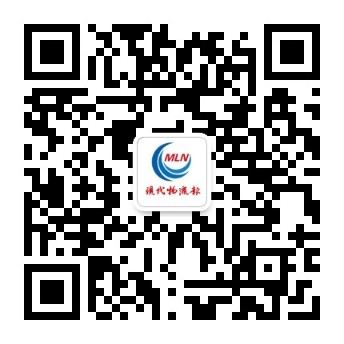
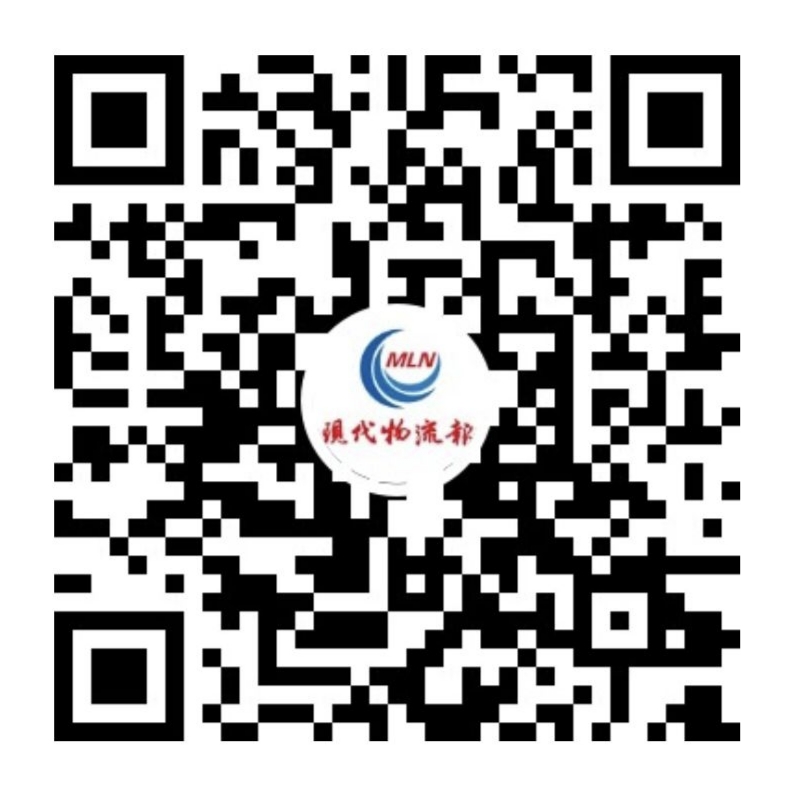
相关文章: